The increase in demand for flexible electronics has forced engineers to rethink how circuit boards are built. Technology like wearable devices, medical sensors, and smart textiles require an incredible amount of malleability and stretchability, which has challenged the traditional rigidity of electronic components.
In an effort to help electronics become truly stretchable, a research team examined liquid metal and its ability to be 3D-printed as a way to retain conductivity at high deformation.
“Researchers have made significant advances in fabricating stretchable wires using looped or serpentine metal traces, stretchable conductive links, and encapsulated liquid metals,” said Matthew Johnston of the research team at the School of Electrical Engineering and Computer Science, Oregon State University. “This work demonstrates an ability to 3D-print free-standing stretchable metal wires on top of a silicone substrate to enable layer-by-layer fabrication of stretchable printed circuits.”
The team first determined that a liquid metal paste would be ideal for manufacturing stretchable electronics. It doesn’t require a mold, can work across a variety of arbitrary geometries, has a conductivity about an order of magnitude less than copper, and has the ability to be 3D-printed. Additionally, it improves mechanical stability and rheological properties favorable for extrusion.
To produce the paste, which is nickel-based, solids are introduced into the pure gallium alloy. Eutetic gallium alloy is loaded on top of metal powder, and sonication energy is applied to mix the powder into the liquid phase. A detailed illustration of the production process can be seen below in Figure 1.
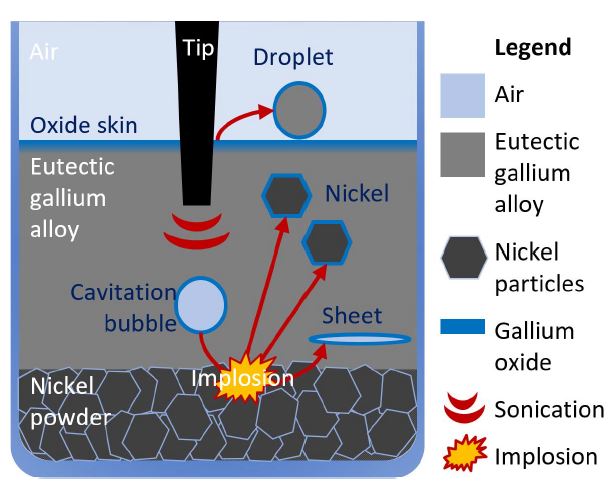
Figure 1: Liquid Metal Paste Production Process
After the paste was developed and its conductivity was tested, the team test printed electronic objects with a commercial 3D printer. An LED oscillator circuit, a passive resistive strain sensor, and a resistive strain sensor with integrated active readout were all test printed to examine the breadth of printable objects. The first demonstrated integration of the paste with active and passive electronic components, the second showed that liquid metal paste retains conductivity during high strain, and the third added optical and digital readout capabilities.
As an example, a full demonstration of the LED oscillator circuit printing can be seen below in Figure 2. The demonstration highlights everything from the schematic and assembly, to its unstretched and stretched states.
Figure 2: Demonstration of 3D-Printing a LED Oscillator Circuit
Having successfully 3D-printed the three electronic objects and tested their functionality, the team was able to prove that there’s a scalable method for the fabrication of stretchable electronics. Plus, the cycle data obtained from testing the printed strain sensors proved that liquid metal paste is a stable conductor under stress and deformation.
Moving forward, the team will work to combine liquid metal paste printing with silicone encapsulations to build 3D silicone shapes with integrated circuitry. They believe there is a critical short-term need for stretchable wires in wearable devices, as well as body-worn medical sensors.
“We will work on improving resolution and yield of the printing process, as well as improving our ability to integrate standard off-the-shelf ICs and passive components into the build process,” said Johnston. “We also have an ongoing effort characterizing the short-term and long-term performance of the stretchable wires. Results have been promising so far, but this is an active area of research for us.”
For more information on 3D printing, visit the IEEE Xplore Digital Library.